Modbus® has been a standard method of communication between industrial devices such as PLCs, sensors, and actuators for decades. It provides a reliable way to exchange data and automate processes. For industries that utilize industrial IoT (IIoT), Modbus® with LoRaWAN® can provide monitoring on another level. VoBo bridges the two, allowing a level of communication that isn’t normally possible. In this article, we’ll explore the advantages of Modbus® and see how VoBo adds a new dimension to industrial monitoring.
What is Modbus®?
Modbus® is a communication protocol that’s used in industrial automation to transfer data between devices. It can operate over serial lines (Modbus® RTU, RS-232, or RS-485) or Ethernet (Modbus® TCP).
Modbus® is comprised of a Client and Server. The Client asks the server for data. The Server then processes the request and provides the data to the Client. One Client can have multiple Servers.
It can work with SCADA systems to exchange data between devices such as PLCs, sensors, and actuators, to allow for remote monitoring and control of industrial processes.
There are many reasons to use Modbus® for industrial automation. Modbus® has a simple client-server architecture. A client device initiates the communication, and the server devices respond with the data.
Industrial devices and instrumentation often have Modbus® serial communication capability. Modbus® allows the primary data to be easily collected from the device along with other useful data, such as status and units.
VoBo Bridges Modbus® to LoRaWAN®
Modbus® does have a few limitations when used in modern industrial environments. Fortunately, these issues can be solved by bridging Modbus® to LoRaWAN®.
Modbus® Issues
- Modbus® requires wired connections. This makes it unsuitable for use over long distances and difficult to scale.
- Modbus® requires physical wiring. This can be expensive, time-consuming, and can cause downtime due to damage.
- Modbus® installations can be complex. This requires specialized knowledge and equipment.
- Modbus®, especially RTU, does not include encryption and authentication, making it vulnerable to hacking and tampering.
How LoRaWAN® Solves These Issues
- LoRaWAN® uses long-range, low-power radio technology. This allows for data transmission over long distances or in noisy industrial environments
- LoRaWAN® enables wireless data collection from remote endpoints. This eliminates the need for wiring, and it simplifies installation.
- LoRaWAN® can support a large number of devices, making it a great choice for large-scale IIoT systems.
- LoRaWAN® offers encryption and authentication, protecting data transmission.
VoBo Connects Modbus® to LoRaWAN®
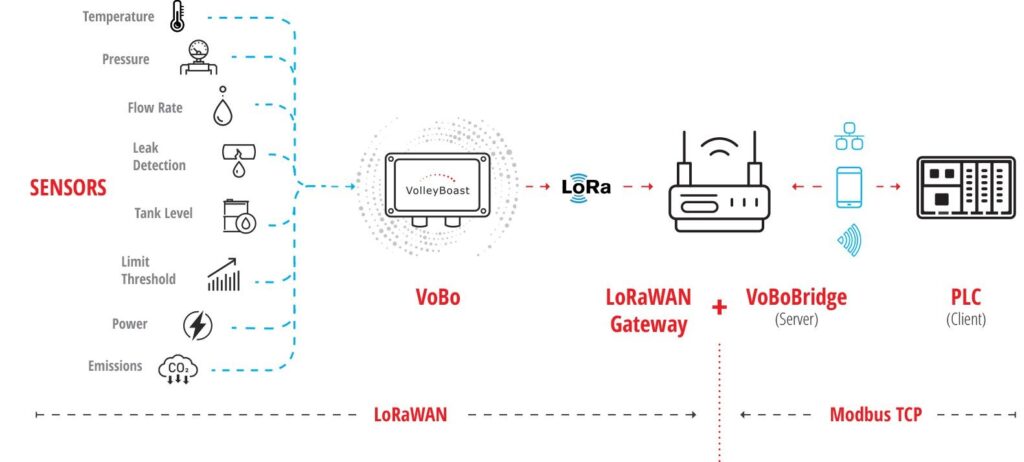
LoRaWAN® solves the issues with Modbus®, but to work with LoRaWAN®, Modbus® needs a bridge to connect the two technologies. VoBo serves as a powerful bridge that integrates Modbus® devices with LoRaWAN® networks.
VoBo Enhances Modbus® Systems
VoBo integrates Modbus® devices with LoRaWAN® networks. This allows for efficient data collection and transmission to a LoRaWAN® network.
Features Include:
- VoBo can read from and write to RS-485 Modbus® RTU devices. This creates smooth communication between Modbus® devices and servers.
- VoBo can write directly to a Modbus® device’s registers when required. This allows the VoBo to instruct a server device to do something that is required for data collection.
- The VoBo payload decoder works across LoRaWAN® network servers and supports Modbus® word and byte swap functionality.
- A single VoBo can read and write data to multiple daisy-chained Modbus® devices, creating efficiency.
- A VoBo can collect data from analog, digital, and Modbus® devices at once.
VoBoBridge Enables Modbus® TCP Connectivity
VoBoBridge extends VoBo’s capabilities by adding Modbus® TCP/IP support at the gateway. Modbus® RTU and TCP protocols can be utilized within different segments of the same data stream.
A VoBo reads Modbus® RTU devices and transmits that data via LoRaWAN® to the VoBoBridge. The VoBoBridge then interfaces with a SCADA system over Modbus® TCP/IP.
VoBoAnalytics Provides Edge Processing
VoBoAnalytics gives the VoBo edge computing capabilities, allowing for data processing and insights at the network edge. User-defined algorithms onboard the VoBo can be applied to one or multiple Modbus® RTU data channels.
The result of analytics on the Modbus® data can be to transmit data, adjust configurations, or write values to Modbus® registers.
Read Multiple Data Channels
Modbus® RTU over RS-485 is a serial connection that allows one client to communicate a request for register data from one or multiple servers.
Common analog sensors output a single data channel. Collecting data in this manner is effective, but when more complex devices, with complex measurements producing many points of data are utilized, serial communication is the most effective means to collect it. One of the advantages of Modbus® is the ability to collect data from many registers during a read cycle. It works by allowing a Modbus® client to poll various server devices, such as controllers, sensors, inverters, and other instrumentation.
Modbus® for Instantaneous Flow and Totalized Flow
Flow meters and Flow Totalizers often have Modbus® RTU serial communication capability and can be used to collect instantaneous and totalized flow. Flow totalizers, which are often used with turbine flow meters, can provide both instantaneous flow rates and accumulated totals.
Instantaneous flow refers to the current flow rate at a specific moment in time. It is measured and recorded in a flow meter’s register data.
A flow totalizer accumulates the total flow of a fluid over a period of time. It provides a running total of the volume that’s passed through a system.
The VoBo can work with many flow meters and totalizers, using Modbus® communication to read both the instantaneous and the totalized flow data. This data is critical information for process monitoring.
Industrial Applications of VoBo with Modbus®
There are many industrial applications with VoBo and Modbus®. Here’s a look at a few:
Manufacturing – Automate processes, monitor equipment condition, and optimize production lines without complex wiring.
Process Quality – Monitor process parameters throughout the system.
Steam Systems – Monitor heat trace controllers, their operation, and alert maintenance.
Power Systems – Remote monitor generators, transformers, and energy distribution systems with a VoBo.
Emissions – Monitor the number of emissions for compliance with safety requirements.
Water Management – Monitor water levels, flow rates, and pump controller parameters.
Conclusion
Modbus® is a widely used communication protocol for industrial automation. VoBo revolutionizes industrial Modbus® communication by integrating it with LoRaWAN®, providing scalability, cost savings, and remote monitoring capabilities. Regardless of your industrial Modbus® needs, VoBo ensures that your Modbus® devices remain connected.
Visit VolleyBoast to explore how VoBo can enhance your Modbus® applications.