Industrial IoT is rapidly evolving, and LoRaWAN® has become a popular wireless communication protocol for long-range, low-power implementations. However, with so many hardware and network options available, choosing the right LoRaWAN® solution for your needs isn’t always straightforward. Whether you’re just starting with a proof of concept or deploying at scale, here are nine factors to consider when planning your LoRaWAN® solution.
1. Is It Proof of Concept or Is It Ready for Deployment?
The first step is understanding your project’s maturity. Are you experimenting with a new idea or scaling up for real-world operations? A proof of concept (PoC) might prioritize flexibility and rapid implementation, even if the setup is temporary or limited. A solution that’s ready for production should be hardened and meet all of the environmental and operational standards. Select the hardware and network infrastructure that matches your phase. Overbuilding too early can waste resources, while underbuilding during deployment can stall your progress.
2. Is a LoRaWAN® Network Already Available, or Do You Need to Install One?
Before selecting your LoRaWAN® devices, determine whether there is existing LoRaWAN® network coverage at your site. If not, you’ll need to plan for gateway placement and network infrastructure. Some solutions can piggyback on public or shared networks, while others may require a private network for full control and reliability. Consider the coverage, range, network density (number of sensors, gateways, servers, etc.), and security requirements. A product like a VoBo can bridge the gap, especially when paired with a private gateway in remote or industrial areas. A site survey of the coverage area will guide gateway and endpoint placement.
3. Are the Sensors Already Installed but Not Connected?
Many facilities already have legacy sensors in place that aren’t connected to the network. Rather than replacing working sensors, consider VoBo LoRaWAN® endpoint bridges that can retrofit the existing equipment. A VoBo can interface with analog, discrete, or RS485 Modbus RTU outputs, which can give legacy sensors a new life on modern networks. This saves cost, simplifies installation, and is scalable.
4. Do the Sensors Have a Wired Output?
If the sensor has a wired output, such as 4-20 mA, Modbus, or a dry contact, ensure that your LoRaWAN® endpoint supports that protocol. Not all LoRaWAN® devices are created equal. The right endpoint bridge, such as a VoBo, will translate these signals into LoRaWAN® messages without the need for converters or complicated setups. This compatibility can be the difference between an easy and quick installation and a frustrating integration.
5. Is Local Power Available or Do You Need a Self-Powered Solution?
Power is one of the most critical questions when choosing a LoRaWAN® solution. If there’s no power nearby, your LoRaWAN® endpoint must be battery-operated, and it will need to power the sensor itself. Devices like the VoBo come with an internal battery and can power many sensors for years at a time. On the other hand, if power is available, you might choose an endpoint without an internal battery, such as the VoBo XP, and gain continuous operation and downlink listening.
6. Do You Need Hazardous Location Certification?
Industrial sites often require equipment to meet hazardous area ratings such as Class I, Division 2 in the US and Canada. If you’re operating in a hazardous environment, make sure your LoRaWAN® device is properly certified. Not having the proper rating can be a safety risk and violate regulatory compliance. Choose your endpoints based on your certification needs. Even if you don’t need hazardous certification, you might still need rugged equipment that can withstand the elements. All VoBos include rugged enclosures to protect against water and dust.
7. What Are You Measuring?
Not all LoRaWAN® devices are made for the same data types. Are you reading pressure, temperature, flow, vibration, or a switch status? Each measurement may require a different type of sensor interface and data format. For example, differential pressure might need a high-resolution analog input, while a float switch just needs a digital input. Choose hardware that’s designed for your sensing needs and ensure that your LoRaWAN® solution supports the data format and resolution needed.
8. How Often Do You Need to Read the Data?
LoRaWAN® is great for low-frequency transmissions, but every application has different timing needs. Do you need to take a data reading every few minutes, every hour, or just when something changes? More frequent data readings require more power and more airtime, which impacts your device’s battery life and the network capacity. Choose a device that can be configured to match the frequency of your data reading needs and make sure the network can handle it efficiently.
9. What Is the Objective?
What problem are you trying to solve? Are you looking for early fault detection, process optimization, regulatory compliance, or safety monitoring? Your end goal should shape every aspect of your LoRaWAN® system, from how often you collect data to where it’s stored or utilized. Always build or expand your system based on your goals. Aligning the technical solution with your business objectives ensures that your efforts provide a Return on Investment (ROI) that matches your objectives.
Why VoBo Is a Strong Fit
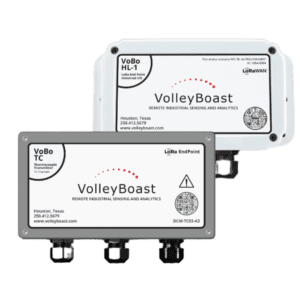
If you’re looking for a flexible, reliable, and field-proven LoRaWAN® endpoint bridge, the VoBo integrates with any LoRaWAN® network.
- PoC to Production – VoBo is simple enough for prototyping, and it’s also rugged enough for real-world usage.
- Network Flexibility – Whether you’re joining an existing LoRaWAN® network or deploying your own, VoBo is sensor-agnostic and integrates easily.
- Retrofit-Ready – If you already have sensors installed, a VoBo can interface with your 4-20 mA, discrete, serial, and other wired outputs to bring them online without replacing them.
- Wired Input Support – VoBo supports a variety of sensor outputs, making it ideal for both simple and complex installations.
- Battery-Powered and Sensor-Powering – With its internal battery, a VoBo can operate independently for years and even power its connected sensors.
- Hazardous Location Options – VoBo models are available with hazardous location certifications such as Class I, Division 2. This is perfect for oil and gas or chemical facilities.
- Versatile Connections – Whether you’re monitoring pressure, level, temperature, or switch status, VoBo is highly compatible and flexible enough to handle the most common signal types.
- Aligned With Your Goals – VoBo is built with real operational goals in mind, whether it’s leak detection, preventive maintenance, or compliance reporting.
Conclusion
LoRaWAN® offers incredible flexibility for connecting sensors in hard-to-reach places, but the best solution depends on your specific use case. By addressing these nine considerations, from network availability and power to measurement type and end goals, you can avoid common pitfalls and build a smarter, more scalable IoT system. Whether you’re retrofitting a legacy infrastructure or launching a brand-new LoRaWAN® system, asking the right questions up front will save time, money, and headaches down the road.
For more information, visit the VoBoAnalytics page or contact info@volleyboast.com.